Inventory analysis is a critical component of supply chain management and involves examining inventory data to optimize stock levels, reduce holding costs, and improve overall business efficiency. Here are some essential tools and techniques for effective inventory analysis:
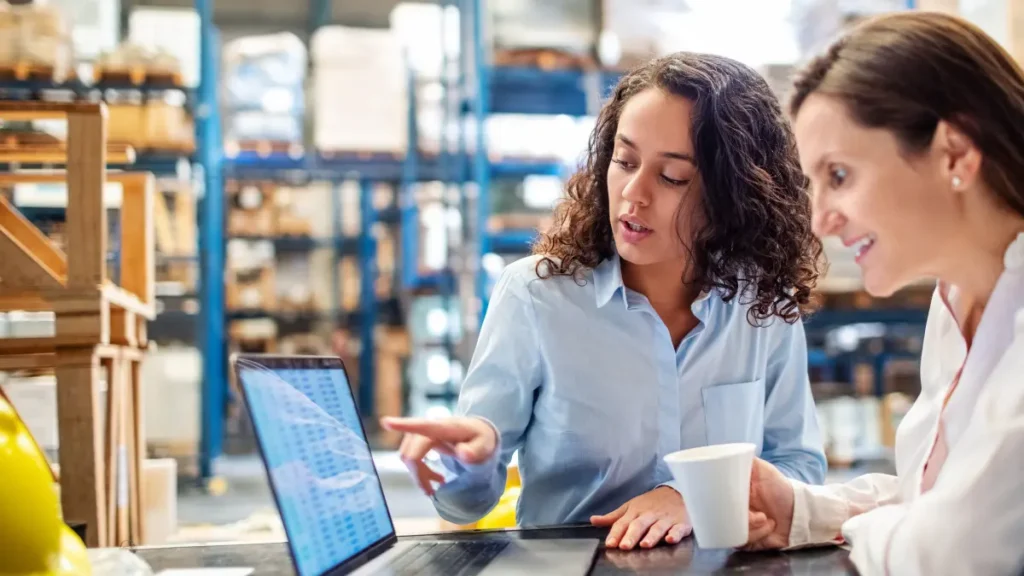
Tools for Inventory Analysis
Effective inventory management relies on robust tools to streamline operations and enhance visibility across supply chains. Let us understand tem in detail.
1. Inventory Management Software
- ERP Systems: ERP systems like SAP, Oracle, and Microsoft Dynamics offer a comprehensive solution for managing all aspects of a business, including inventory. These systems integrate inventory management with other business processes such as sales, finance, and supply chain management. Benefits include real-time data visibility, automation of inventory-related tasks, and improved accuracy in inventory tracking.
- Standalone Inventory Management Software: Tools such as Zoho Inventory, TradeGecko, and QuickBooks Commerce are specifically designed for inventory management. They provide features like order management, stock tracking, and reporting. These tools are often more affordable and easier to implement than full ERP systems, making them ideal for small to medium-sized businesses.
2. Spreadsheet Software
- Microsoft Excel and Google Sheets: These are powerful tools for managing and analyzing inventory data. They allow users to create custom spreadsheets for tracking inventory levels, calculating metrics, and generating reports. Spreadsheets are flexible, customizable, and widely accessible, making them ideal for small businesses or specific tasks that do not require the complexity of dedicated inventory management software. Advanced features like pivot tables, charts, and formulas enable detailed data analysis.
3. Business Intelligence (BI) Tools
- Tableau, Power BI, and Looker: BI tools are used to visualize and analyze inventory data, creating interactive dashboards. They can connect to multiple data sources and provide advanced analytics capabilities to identify trends and patterns. BI tools help in identifying trends, patterns, and anomalies in inventory data, supporting data-driven decision-making by providing actionable insights.
4. Barcoding and RFID Systems
- Functionality: Barcoding and Radio Frequency Identification (RFID) systems automate the process of tracking inventory. Each item is assigned a unique barcode or RFID tag, which can be scanned to update inventory records. These systems enhance accuracy and efficiency in inventory tracking, reduce manual errors, speed up the receiving and shipping processes, and provide real-time visibility into inventory movements.
5. Warehouse Management Systems (WMS)
- Manhattan Associates, JDA, and HighJump: WMS software is designed to optimize warehouse operations. It manages the storage, movement, and picking of inventory within a warehouse. WMS systems improve warehouse efficiency by optimizing space utilization, reducing pick times, and improving order accuracy. They provide real-time visibility into warehouse activities and help streamline processes such as receiving, putaway, picking, and shipping.
Techniques for Inventory Analysis
Implementing strategic techniques is essential for gaining actionable insights into inventory data. Few of the commonly used methods are given below.
1. ABC Analysis
ABC Analysis categorizes inventory into three classes based on their importance:
- Class A: High-value items that account for a significant portion of the inventory value but are small in quantity. These items require stringent control and accurate records.
- Class B: Moderate value items that fall between Class A and C in terms of value and quantity. These items require moderate management efforts.
- Class C: Low-value items that are large in quantity but account for a small portion of the inventory value. These items require simpler controls.
This classification helps prioritize management efforts and resources according to the significance of each class.
2. Economic Order Quantity (EOQ)
EOQ is a formula used to determine the optimal order quantity that minimizes the total cost of ordering and holding inventory. It considers the annual demand, ordering cost per order, and holding cost per unit per year. By calculating the EOQ, businesses can find the most cost-effective quantity to order, reducing both order and holding costs.
3. Just-In-Time (JIT) Inventory
JIT is an inventory strategy that aims to reduce holding costs by receiving goods only as they are needed in the production process. This minimizes the amount of inventory on hand and reduces waste. JIT requires a strong relationship with suppliers and accurate demand forecasting to be effective.
4. Safety Stock Analysis
This tool determines the appropriate level of extra inventory to hold to protect against stockouts due to demand variability or supply delays. Safety stock acts as a buffer to ensure that there are enough products available to meet customer demand even when there are fluctuations in demand or supply chain disruptions.
5. Demand Forecasting
Demand forecasting uses historical sales data, market trends, and statistical methods to predict future demand. Accurate demand forecasting helps businesses adjust inventory levels to meet anticipated demand, avoiding both stockouts and overstock situations. Techniques can include time series analysis, regression analysis, and machine learning models.
6. Inventory Turnover Ratio
The Inventory Turnover Ratio measures how often inventory is sold and replaced over a period. It is calculated by dividing the cost of goods sold by the average inventory. A higher turnover ratio indicates efficient inventory management and suggests that products are being sold quickly, while a lower ratio may indicate overstocking or slow-moving inventory.
7. Lot Tracking and Traceability
Lot tracking and traceability involve tracking inventory by lot or batch numbers to ensure accurate records of production and distribution. This is especially important in industries like food and pharmaceuticals where traceability is crucial for compliance and safety. Lot tracking helps in identifying and isolating specific batches in case of recalls or quality issues.
8. Reorder Point Formula
The Reorder Point Formula calculates the inventory level at which a new order should be placed to avoid stockouts. It considers the lead time for delivery and the average daily usage of inventory. The reorder point ensures that there is enough stock available to meet demand during the lead time.
9. Cycle Counting
This tool is a periodic counting of a subset of inventory items to maintain accurate inventory records without shutting down operations for a full physical inventory count. Cycle counts can be done daily, weekly, or monthly, and are often focused on high-value or high-movement items. This technique helps in identifying discrepancies and maintaining inventory accuracy.
10. Six Sigma
Six Sigma is a set of techniques and tools for process improvement that can help identify and eliminate defects in inventory management processes. It focuses on reducing variability and improving quality through a disciplined, data-driven approach. Six Sigma methodologies, such as DMAIC (Define, Measure, Analyze, Improve, Control), can be applied to inventory management to enhance efficiency and accuracy.
11. Pareto Analysis
Pareto Analysis, also known as the 80/20 rule, is a technique used to identify the most significant factors affecting inventory levels. It is based on the principle that 80% of the effects come from 20% of the causes. By focusing on the critical 20% of items that contribute to 80% of sales or value, businesses can prioritize their inventory management efforts and resources more effectively.
12. Inventory Aging Reports
Inventory Aging Reports show the age of inventory items, helping to identify slow-moving or obsolete stock. These reports categorize inventory based on how long items have been in stock, such as 0-30 days, 31-60 days, and so on. This information is crucial for managing stock levels, planning promotions or clearance sales, and avoiding holding costs for unsellable inventory.
2 Comments