If your supply chain spans multiple warehouses, plants, or distribution centers, you’ve probably faced this costly problem: too much inventory sitting idle in one location while another scrambles to fill urgent orders. This imbalance drives up costs, slows deliveries, and frustrates customers. Risk pooling is the strategy that fixes it.
In this guide, you’ll learn how risk pooling in multi-echelon supply chains works, why it’s becoming a go-to tactic for supply chain leaders in 2025, and the exact steps you can take to cut costs, avoid stockouts, and boost service levels — all without bloating your safety stock.
What is Risk Pooling in Supply Chain?
Risk pooling in supply chain management — sometimes called inventory pooling — is the practice of consolidating resources such as inventory, production capacity, or demand across different locations or business units. The goal is to reduce variability, improve efficiency, and ensure no single location is left overstocked or understocked. In simple terms, it’s about sharing the “risk” of demand fluctuations so your network as a whole performs better.
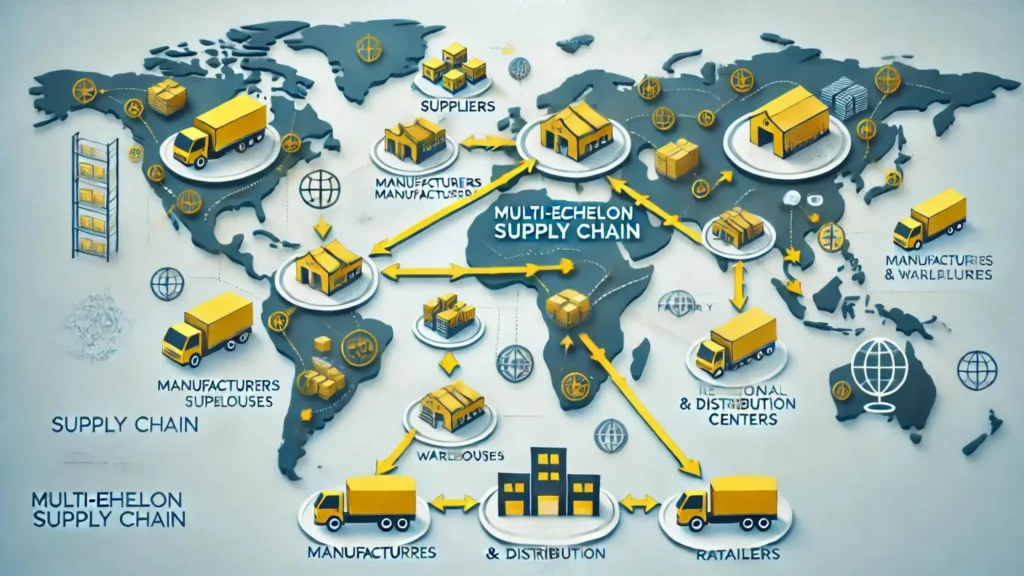
Example:
Imagine three regional warehouses, each stocking the same product. If each operates independently, one might run out of stock while another has excess inventory. By pooling inventory into a central hub that serves all regions, you can meet demand more evenly and reduce the total safety stock needed.
A visual way to think about it:
Picture an office building where each department buys its own umbrellas for rainy days. Some teams end up with dozens unused, while others run out when storms hit. If the whole building shares one central umbrella stand, everyone has a better chance of staying dry without overspending.
Why it matters in multi-echelon networks:
In a multi-echelon supply chain—where goods move through multiple tiers like factories, distribution centers, and retail outlets—risk pooling can smooth out demand variability at every stage. This leads to:
- More predictable service levels, even during demand spikes or supply disruptions
- Lower total inventory investment
- Fewer stockouts across the network
Types of Risk Pooling
Risk pooling isn’t a one-size-fits-all concept. In supply chain management, it can take several forms, each targeting a specific source of uncertainty. Understanding these variations will help you decide which approach best fits your network.
Inventory Risk Pooling
This is the most common type, where inventory is consolidated from multiple locations into a central facility. The goal is to reduce safety stock while still meeting service levels.
Example: A retailer moving safety stock from ten regional stores into one central distribution center.
Capacity Pooling
Here, production or transportation capacity is shared across different locations or product lines. It helps balance workloads and avoid idle capacity in one area while another struggles to keep up.
Example: Two plants producing similar products agree to share overflow orders during peak season.
Demand Pooling
This involves combining demand forecasts from multiple sources to create a more accurate and less variable forecast. Aggregating data across regions smooths out spikes and dips.
Example: A global electronics company pooling demand forecasts from Asia, Europe, and North America to plan global production runs.
Lead Time Pooling
Instead of relying on a single supplier or transport route, multiple sources are used to reduce the risk of long delays.
Example: An apparel brand sourcing zippers from two suppliers in different regions to avoid disruption if one faces production issues.
How Multi-Echelon Risk Pooling Works?
A multi-echelon supply chain is made up of multiple stages — such as factories, central distribution centers, regional warehouses, and retail outlets — that work together to deliver products to the customer. Each echelon carries some level of inventory and faces its own demand variability.
Risk pooling in a multi-echelon network focuses on reducing that variability by consolidating resources and coordinating inventory policies across tiers, rather than managing each location in isolation.
Step-by-Step Example
- Single-Echelon Scenario – Imagine each regional warehouse forecasting demand and holding safety stock independently. This often leads to overstock in some regions and shortages in others.
- Multi-Echelon Approach – Instead of treating each warehouse as a silo, inventory buffers are pooled at higher levels in the chain (such as a central DC). These pooled inventories serve multiple regions, which helps absorb local demand swings without excessive stock everywhere.
- Flow of Goods – Factories replenish the central DC based on aggregated demand, and the DC allocates stock to regional warehouses dynamically, depending on real-time needs.
Why it works:
- Aggregating demand across locations reduces the overall variability (a statistical effect known as the “square root law” in inventory management).
- Centralized control enables better prioritization when stock is limited, ensuring the highest-impact orders are fulfilled first.
- Technology, such as multi-echelon inventory optimization (MEIO) software, makes it possible to model the entire network and set stocking policies that minimize total system cost while maintaining service levels.
In short, multi-echelon risk pooling transforms the supply chain from a set of disconnected islands into a coordinated network — one that’s leaner, faster, and better prepared for uncertainty.
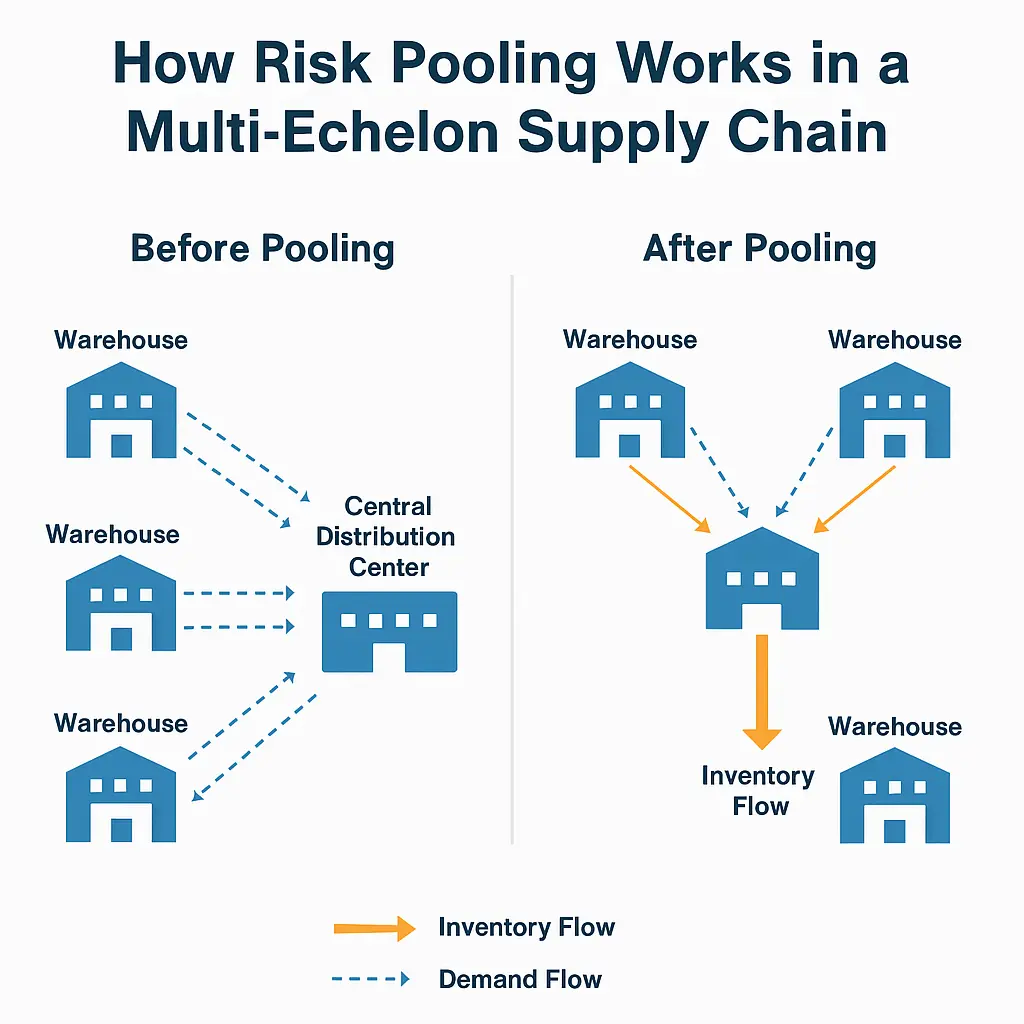
Benefits of Risk Pooling in Supply Chain
When implemented effectively, risk pooling in supply chain management can deliver measurable gains in cost efficiency, service quality, and operational resilience. By consolidating resources and reducing variability across the network, businesses can make better use of inventory, improve customer satisfaction, and lower overall risk.
1. Lower Safety Stock Requirements
Pooling inventory from multiple locations into centralized hubs reduces the total safety stock needed while still protecting against demand fluctuations.
Example: A central distribution model can cut safety stock by 15–30% compared to holding separate buffers at each regional warehouse.
2. Fewer Stockouts and Lost Sales
Shared inventory pools make it easier to reallocate products quickly to regions experiencing a demand surge. This prevents costly stockouts and protects revenue.
Example: During a holiday rush, a retailer using pooled inventory fulfilled 98% of orders, compared to 90% with isolated stock.
3. More Accurate Demand Forecasts
Aggregating demand data from multiple echelons smooths out local spikes and dips, creating more stable and reliable forecasts. This leads to smarter replenishment decisions and better service levels.
4. Cost Savings in Storage and Handling
With less safety stock, businesses can reduce warehouse space, lower handling costs, and minimize insurance and obsolescence expenses.
5. Stronger Supply Chain Resilience
Pooling inventory, capacity, or demand allows businesses to adapt faster when disruptions occur — whether that’s a supplier delay, a transportation bottleneck, or an unexpected demand spike.
Best Practices for Risk Pooling in Multi-Echelon Supply Chains
Effective risk pooling isn’t just about moving inventory around — it’s about building a system that balances efficiency with customer service. These best practices will help you get the most out of your multi-echelon risk pooling strategy.
1. Centralize Where Variability Is Highest
Identify products or locations with the greatest demand fluctuations and centralize inventory for those first. This gives you the biggest impact on reducing safety stock.
2. Use Advanced Forecasting and Analytics
Leverage demand forecasting tools and multi-echelon inventory optimization (MEIO) software to simulate different pooling scenarios. This data-driven approach ensures that decisions are based on actual variability and cost trade-offs.
Internal link idea: Link to your Supply Chain Analytics Guide or Forecasting Tools article.
3. Balance Pooling With Service Commitments
While centralizing stock cuts costs, it can add lead time. Maintain service-level agreements (SLAs) by strategically placing “fast movers” closer to the customer.
4. Monitor Lead Time Variability Across Nodes
Track supplier and transportation lead times at each echelon. Even with pooled inventory, inconsistent replenishment can erode the benefits.
5. Integrate Technology and Real-Time Visibility
Use integrated ERP and visibility platforms to track inventory across the network. Real-time data lets you shift inventory proactively when demand changes.
6. Pilot Before Scaling
Start with a small product group or region, measure results, and refine your pooling strategy before rolling it out across the network.
Tools & Technology for Risk Pooling in 2025
Risk pooling delivers the best results when backed by the right technology. In 2025, supply chain teams have access to advanced software and platforms that make multi-echelon risk pooling faster to design, easier to monitor, and more cost-effective to maintain.
Multi-Echelon Inventory Optimization (MEIO) Software
Platforms like SAP Integrated Business Planning (SAP IBP), o9 Solutions, and Kinaxis RapidResponse allow you to model your entire network, simulate pooling strategies, and set optimal stocking policies across all echelons.
AI-Powered Demand Forecasting
Machine learning models, available in tools such as ToolsGroup SO99+ or Blue Yonder Luminate, aggregate and analyze demand from multiple sources to create more accurate, less volatile forecasts.
Real-Time Visibility Platforms
Solutions like project44, FourKites, and Shippeo offer end-to-end visibility on inventory location, in-transit shipments, and potential delays — enabling proactive inventory reallocation.
Integrated ERP Systems
Systems like Oracle NetSuite or Microsoft Dynamics 365 Supply Chain help unify inventory, sales, and procurement data, ensuring every echelon works from the same real-time information.
Simulation & Scenario Planning Tools
Platforms such as AnyLogic or Arena Simulation let you stress-test your pooling strategy against various demand and supply disruption scenarios before making costly changes in the real world.
Pro Tip: Even small and mid-sized businesses can benefit — many of these solutions now offer modular, cloud-based versions with lower upfront investment, making them more accessible than ever.
Challenges & How to Overcome Them
While risk pooling in supply chain management offers clear benefits, it’s not without its hurdles. Recognizing these challenges early — and knowing how to address them — can make the difference between a smooth rollout and a costly misstep.
1. Coordination Complexity
Pooling resources requires tight coordination between different echelons, functions, and even business units. Misaligned priorities can cause delays and inefficiencies.
How to Overcome: Establish a centralized planning team or “control tower” that oversees all pooled resources and sets unified inventory policies.
2. Resistance to Change
Local warehouses or sales teams may resist pooling if they fear losing autonomy or service speed.
How to Overcome: Start with a pilot project, share results transparently, and involve local teams in planning to build trust.
3. Increased Lead Times
Centralizing inventory can sometimes lengthen delivery times to end customers, especially for fast-moving items.
How to Overcome: Keep high-demand SKUs strategically located closer to customers while pooling slower-moving items.
4. Data Visibility Gaps
Without real-time, accurate inventory and demand data, pooling decisions can lead to shortages or overstock.
How to Overcome: Invest in ERP systems, IoT sensors, or visibility platforms that give all stakeholders the same up-to-date information.
5. Overreliance on a Single Pool
If all stock is consolidated in one location, a disruption there (e.g., natural disaster, labor strike) can halt supply.
How to Overcome: Use multiple pooling points or hybrid strategies to spread risk while keeping efficiency gains.
Case Studies & Real-World Examples
Seeing risk pooling in action makes it easier to understand its real impact. These examples show how companies across industries have applied the concept to cut costs, improve service levels, and build resilience.
Case Study 1: Procter & Gamble (P&G) – Reducing Stockouts by 25%
P&G operates one of the largest consumer goods supply chains in the world, with multiple echelons from plants to retail outlets. By pooling inventory at regional hubs rather than holding large buffers at each store, P&G improved product availability and reduced stockouts by 25% in key markets. The shift also lowered safety stock levels without compromising delivery speed.
Case Study 2: Global Electronics Manufacturer – Saving $15M in Carrying Costs
A leading electronics brand with factories in Asia and distribution centers across North America consolidated its slow-moving product lines into two central hubs. This multi-echelon risk pooling strategy reduced excess inventory, cut annual carrying costs by $15 million, and improved forecast accuracy for niche SKUs.
Case Study 3: Pharmaceutical Distributor – Faster Response to Demand Spikes
A large pharma distributor serving multiple hospitals and clinics faced unpredictable demand during flu season. By pooling critical medicines at a central facility and dynamically allocating stock to local warehouses, they met 99% of urgent orders within 24 hours — a service improvement that was impossible under their previous decentralized model.
Conclusion: Making Risk Pooling Work for Your Supply Chain
Risk pooling in supply chain management isn’t just a cost-cutting tactic — it’s a strategic approach to building a leaner, more resilient, and more responsive network. By consolidating resources, reducing variability, and improving visibility across multiple echelons, companies can lower inventory costs, reduce stockouts, and boost customer satisfaction.
The key to success lies in starting small, using data-driven insights, and scaling your strategy as you prove results. Whether you’re centralizing inventory, pooling capacity, or aggregating demand forecasts, the principles remain the same: plan collaboratively, invest in the right technology, and monitor performance continuously.
If you’re ready to put risk pooling into action, explore tools like our ABC Analysis Calculator, EOQ Calculator and Safety Stock Calculator to optimize inventory decisions and support your next supply chain transformation.
External Resources
A Practical Approach to Supply Chain Risk Management (McKinsey)
This McKinsey article provides insights into risk pooling strategies and their role in managing inventory efficiently across a supply chain:
Evaluating Inventory Risk Pooling Strategy for Multi-Echelon Distribution Networks (MIT)
This study by MIT evaluates the implementation of risk pooling in multi-echelon networks, providing a structured decision-support model:
Multi-Echelon is the Future of Competitive Supply Chains (Supply Chain Digital)
This article emphasizes the benefits of multi-echelon inventory strategies and how they can reduce costs and improve service levels: