Inventory planning is crucial in any supply chain management system. However, theft and fraud can pose significant risks, leading to operational disruptions and financial losses. In fact, shrinkage caused by theft and fraud accounts for approximately 1.5% of retail sales globally, according to the National Retail Federation (NRF). Implementing effective strategies to prevent these issues is essential for safeguarding assets and maintaining smooth business operations.
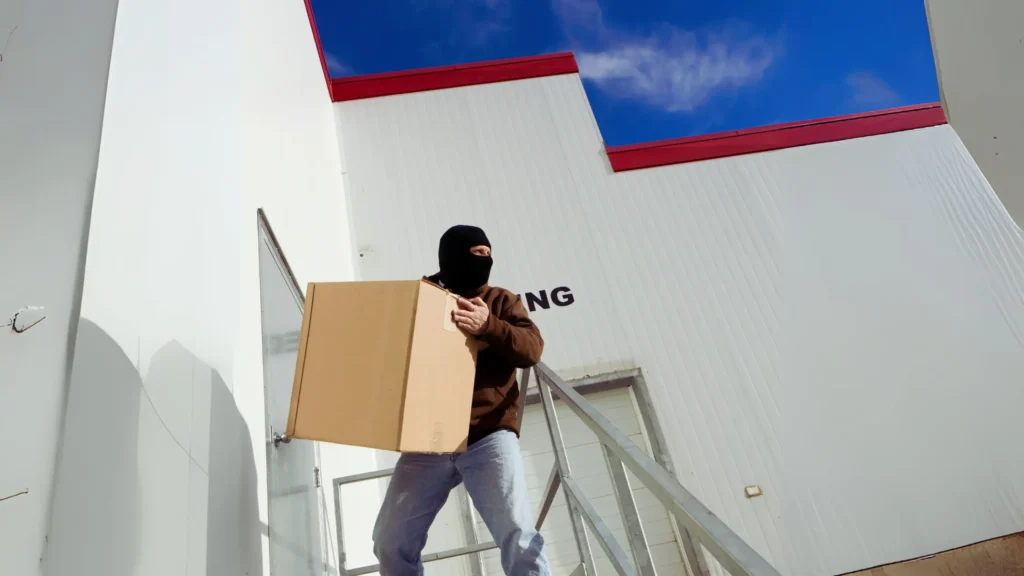
This blog explores key best practices for inventory planning that can help protect your business from theft and fraud, improve operational efficiency, and safeguard your bottom line.
The Importance of Theft and Fraud Prevention in Inventory Planning
Theft and fraud can have significant financial consequences for businesses. Whether from internal sources (employee theft) or external sources (vendor fraud), without proper prevention, theft can lead to unexpected inventory losses. In industries like retail, the average shrinkage rate from theft costs businesses millions annually.
Best Practices for Inventory Planning to Prevent Theft and Fraud
Implementing theft and fraud prevention strategies ensures you maintain inventory accuracy, reduce losses, and build trust with customers, vendors, and stakeholders. Effective inventory management also improves operational efficiency and profitability, ensuring your stock is secure.
Accurate Inventory Tracking Systems
One of the key practices in preventing theft and fraud is implementing accurate inventory tracking systems. Barcode scanners and RFID technologies allow for real-time tracking of items, reducing the chance of manual errors and inventory discrepancies. Automated systems also provide instant updates on stock levels, ensuring transparency and accuracy.
Key Benefits of Accurate Tracking:
- Real-time stock updates: Automated systems eliminate the lag between stock movement and inventory records.
- SKU-level tracking: Track individual items to reduce the risk of loss.
- Warehouse Management Systems (WMS): Integration with WMS allows streamlined inventory tracking, giving visibility into stock levels across multiple locations.
While RFID technology is highly effective, it can be costly for smaller businesses, so it’s essential to weigh the investment against expected benefits. Additionally, consider combining RFID with serial numbers and batch tracking to enhance product-level traceability.
Regular Inventory Audits
Regular inventory audits help identify discrepancies between recorded and actual stock, catching errors early to prevent inventory shrinkage. Depending on the size and complexity of your inventory, audits can range from full annual audits to more frequent cycle counts or spot checks.
Best Audit Practices:
- Cycle counting: This method ensures parts of your inventory are counted periodically without halting operations.
- Variance analysis: Investigate discrepancies between recorded and physical stock.
- Use of mobile audit tools: These tools enable efficient and accurate audits on the go, reducing manual labor and human error.
Auditing frequency may vary depending on industry norms. High-risk industries like luxury goods or electronics might benefit from weekly cycle counts, while bulk goods industries can afford less frequent checks.
Segregation of Duties
Segregating duties across the supply chain ensures that no single person has control over the entire inventory process, thereby reducing opportunities for theft or fraud. In smaller businesses where resources are limited, rotating roles or employing technology-based verifications can serve as effective substitutes for a larger workforce.
Best Practices for Segregation:
- Role division: Ensure that procurement, receiving, and inventory recording are managed by different personnel.
- Dual authorization: Require two-person approvals for large transactions, stock adjustments, or critical decisions.
- Software-based controls: Implement system-based approvals where technology monitors for high-value inventory transactions.
This practice is essential to mitigate risks and provides layers of oversight, which makes internal theft or fraud much harder to execute.
Physical Security Measures
Physical security is a key element of inventory theft prevention. Installing CCTV cameras, access control systems, and employing on-site security personnel can help deter unauthorized access to inventory.
Key Security Measures:
- Surveillance systems: Ensure cameras cover high-risk areas and are actively monitored.
- Restricted access controls: Use keycards, biometric systems, or PIN-based locks to limit access to high-value inventory areas.
- Alarms and sensors: Install alarms and motion sensors to monitor movements during and after work hours.
Modern innovations like geo-fencing or motion-activated cameras are also becoming popular to ensure constant monitoring of valuable stock.
Employee Screening and Training
Employee-related theft often comes from a lack of proper screening or inadequate training on company policies. Conducting background checks for new hires and providing regular training on inventory management processes can minimize internal theft risks.
Key Employee Management Practices:
- Background checks: Ensure that candidates, especially those handling valuable goods, have no prior history of theft or fraud.
- Ongoing training: Regularly train employees on security protocols and ethical behavior, and refresh their understanding of inventory systems.
- Whistleblower systems: Encourage reporting of suspicious behavior through anonymous reporting systems.
Additionally, creating incentive programs that reward employees for reporting suspicious activities can further reduce the likelihood of internal theft.
Data Analysis for Fraud Detection
Leveraging data analytics to monitor stock movement patterns is a powerful tool for detecting fraud. Advanced analytics can identify unusual behaviors or anomalies that might go unnoticed in regular monitoring.
How Data Can Detect Fraud:
- Predictive analytics: Forecast potential risks based on historical data and highlight patterns that suggest fraud.
- Anomaly detection: Identify stock movement patterns that deviate from the norm.
- Stock level monitoring: Pay special attention to high-risk items that may be targeted for theft or manipulation.
AI-based tools and machine learning models are increasingly used to identify fraud faster than traditional methods, flagging irregularities for human review.
Integrated Security Solutions
An Enterprise Resource Planning (ERP) system that integrates inventory, finance, and security measures is key to maintaining consistency across different departments. Integrating inventory management with financial tracking allows companies to monitor discrepancies more efficiently.
Key Features of Integrated Systems:
- Real-time auditing: Automatically create audit trails for all stock movements.
- Financial reconciliation: Cross-check financial transactions with inventory records.
- Automated fraud alerts: Set up notifications for suspicious activity, such as sudden drops in stock levels or unauthorized stock adjustments.
With more businesses adopting IoT-based inventory systems, real-time data collection and integration offer a seamless approach to security.
Vendor and Supplier Verification
Vendor and supplier fraud is a growing concern, making it essential to screen all suppliers rigorously. Conducting regular audits and performing price comparisons can help detect discrepancies or inflated invoicing.
Best Practices for Vendor Verification:
- Regular supplier audits: Evaluate vendors based on delivery performance, pricing, and quality control.
- Vendor rating system: Use a rating system to track performance over time.
- Background checks: Verify vendor legitimacy before entering into long-term agreements.
This prevents fraudulent suppliers from delivering sub-standard goods or inflating invoices, protecting your inventory and finances.
Inventory Turnover and Safety Stock Control
High inventory levels are more prone to theft, which is why monitoring inventory turnover rates is critical. Holding too much stock can make inventory management harder and increase the risk of losses.
Key Inventory Management Strategies:
- Maintain optimal safety stock: Keep safety stock levels high enough to meet demand but low enough to avoid overstocking.
- First-In-First-Out (FIFO): Ensure older inventory moves out first, reducing accumulation and shrinkage.
- Just-In-Time (JIT) inventory: JIT minimizes the risk of theft by reducing stock levels.
Adopting lean management practices reduces the chances of theft and fraud, especially for high-value or perishable items.
Establishing Theft Prevention Policies
Strong policies against theft should be clearly communicated to all employees and suppliers. Your policies should outline ethical guidelines, consequences for dishonest behavior, and steps for reporting and investigating theft.
Key Theft Prevention Policies:
- Code of conduct: Establish ethical standards for all employees.
- Reporting channels: Create secure channels for reporting theft or suspicious behavior.
- Zero-tolerance approach: Clearly define the consequences of theft, including dismissal or legal action.
Having a zero-tolerance policy sends a strong message to all employees and partners, encouraging honesty and integrity in inventory management.
Conclusion
Preventing theft and fraud in inventory management requires a holistic approach, combining technology, employee management, vendor controls, and clear security measures. By implementing the best practices discussed in this blog, businesses can safeguard their inventory, improve operational efficiency, and reduce financial losses.
Start by reviewing your current inventory processes and implement the recommended strategies to ensure your inventory remains protected against theft and fraud.